Insights, Research, News and More...
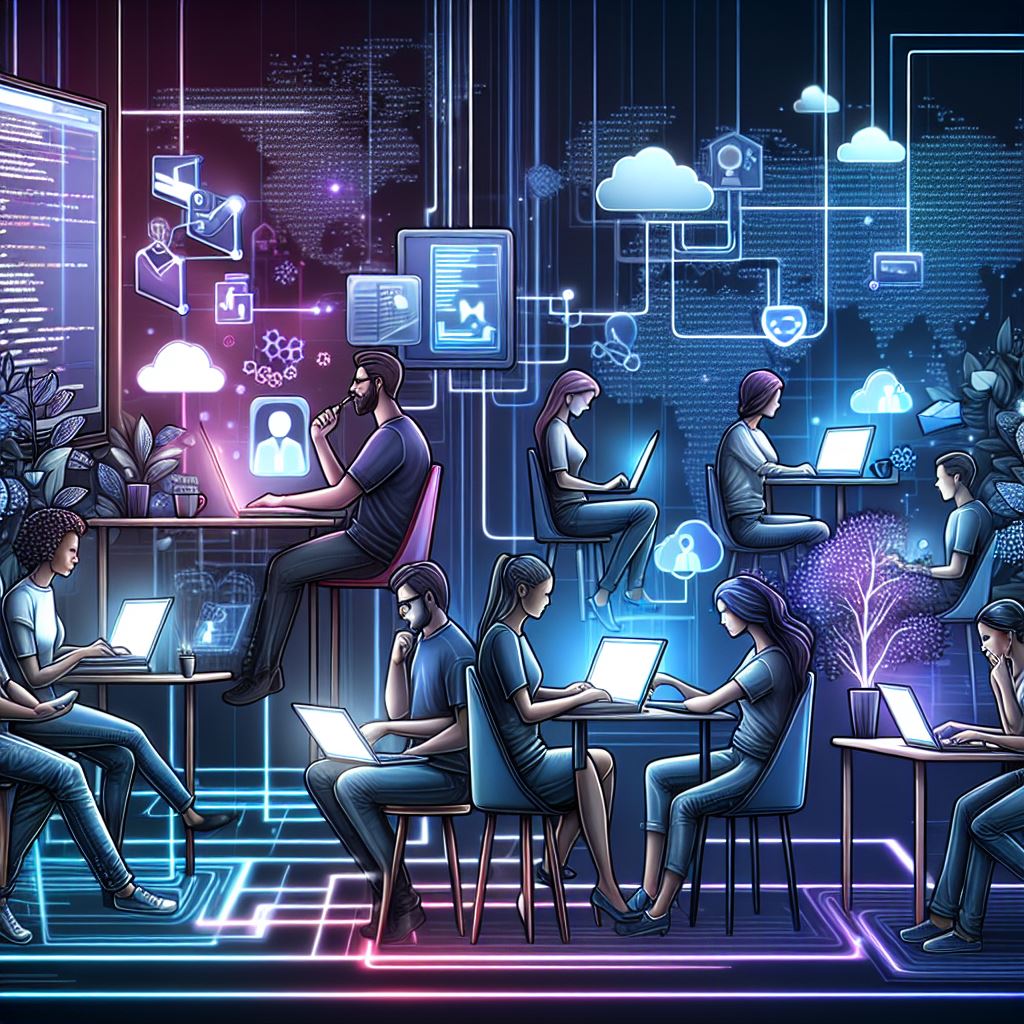
The Knowledge Bottleneck in Chemistry: Why Sharing Skills Is So Hard - And What We Can Do About It
The Knowledge Bottleneck in Chemistry: Why Capturing and Transferring Knowledge Is So Hard
In the scientific world, innovation moves fast - but knowledge doesn’t always keep up. Whether it’s onboarding new chemists, scaling teams across geographies, or transitioning from legacy systems to new, capturing and transferring knowledge remains one of the most persistent challenges in the industry - whether between departments or across entire organizations.
In today’s fast-paced, knowledge-driven economy, scientific organizations are only as strong as the collective expertise of their people.
Why Is It So Difficult?
Despite the abundance of tools and management tactics designed to facilitate knowledge sharing, the process remains stubbornly complex. Here’s why:
1. Tacit Knowledge Is Hard to Document, Sometimes ItLives in Lab Books But Most Of The Time It Lives In People!
Much of the most valuable knowledge in chemistry isn’t written down. It’s embedded in synthetic decisions, previous experience and knowledge, and the mental models of experienced chemists. Chemistry is a heavily manual and practical science after all, which means that most knowledge is gained through experience, intuition, and context.
This kind of knowledge is difficult to articulate, let alone document in a way that others can easily absorb.
This makes it hard to transfer, especially when people leave or teams reorganize.
2. Experimentation Sometimes Outpaces Documentation
The average chemist will setup 1-2 experiments a day, or more if they are screening conditions or creating libraries. The reality of the heavy manual nature of the job means that sometimes it’s faster to just do, than spend the time documenting every decision and thought. Lab books, even when heavily used, are often incomplete and outdated and the information quality of what is captured varies from chemist to chemist. Chemists are left relying on memory, or reverse-engineering past decisions. This leads to a lot of bias while limiting innovation too. It's faster after all to do the same as before, than to figure things out or try new chemistry.
3. Silos Still Exist And Silos Are Specialised
Departments often operate in isolation, with their own language, tools, and priorities. Differences in chemistry specialisation or processes, like R&D and manufacture, or medicinal chemistry and formulation, can often lead to communication gaps, even within the same organisation. This creates barriers to knowledge flow, even when the intent to collaborate is there.
4. Time Constraints
Employees are busy and productivity in the chemical sector is already low. Taking time to document processes, mentor others, or contribute to knowledge bases often falls to the bottom of the priority list - especiallywhen it’s not directly tied to performance metrics.
5. Lack of Incentives
Without clear incentives or recognition, there’s little motivation for individuals to share what they know. Knowledge hoarding can even be seen as a form of job security. The phenomenon of the "golden hands", the one chemist that can execute this reaction better than anyone else is a very common manifestation of knowledge hoarding. This limits innovation and creates organisations that lack practical ownership of their IP.
6. Generic Technology Isn’t a Silver Bullet
While platforms like chat bots, wikis, intranets, ELNs and collaboration tools are helpful, they’re only as effective as the generic models that created them, as well as the culture and processes that support them since their input relies entirely on the user.
What Can Be Done?
To overcome these challenges, organizations need to take a strategic and human-centered approach:
- Foster a culture of learning and sharing by investing in chemists and upskilling them.
- Invest in specialised technology designed specifically for the job, it is a complex one afterall.
- Make standardisation and knowledge capture part of the workflow, without relying on user input.
- Bridge the silos between chemistry specialisations, sites and organisations by utilising the common ground, we are all chemists at the end of the day.
Final Thoughts
Knowledge is one of the most valuable assets an organization has - but only if it is captured and owned. The organizations that thrive in the future will be those that treat knowledge capture and transfer not as a one-time task, but as a continuous, strategic priority.
Want further inspiration? Ask for a demo of our platform to see how we achieved this.
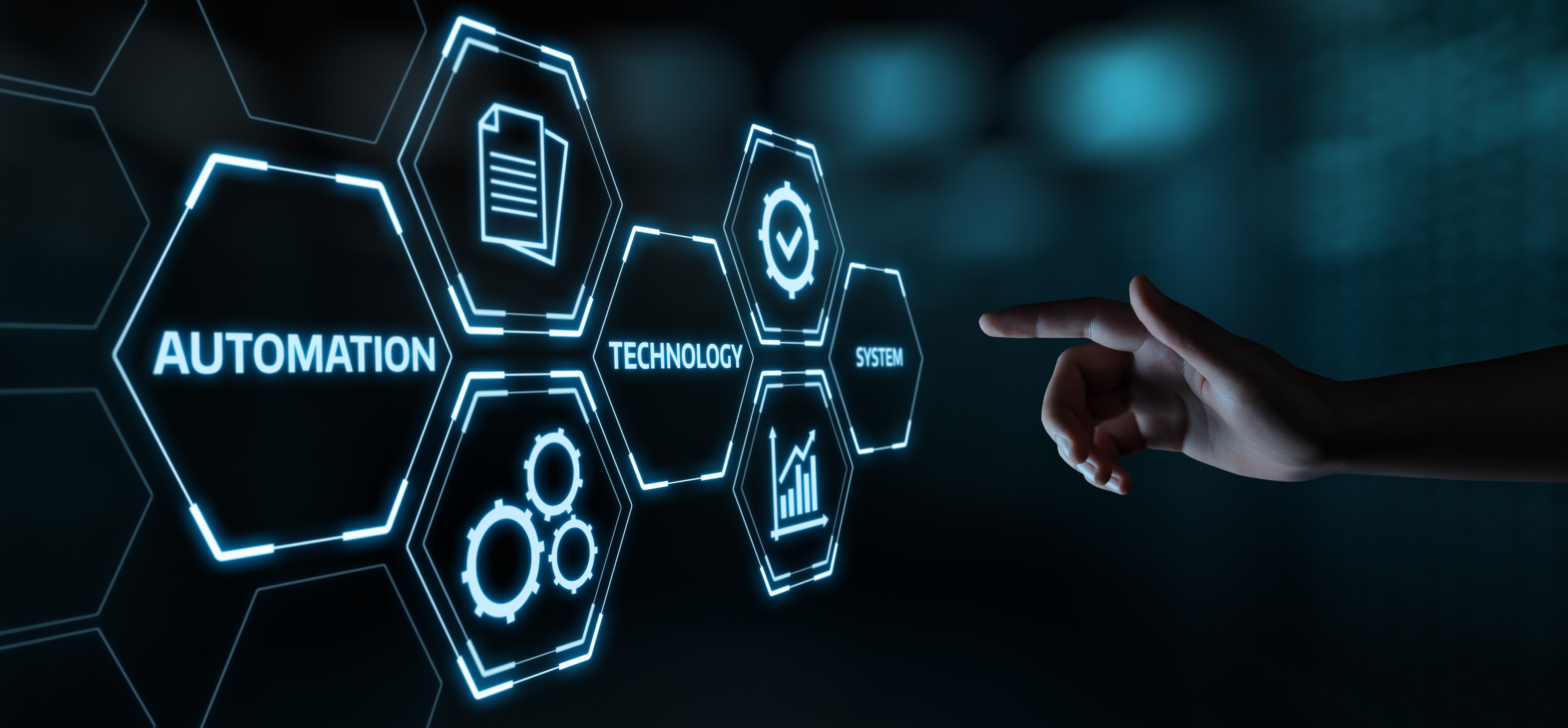
Not all automation is equal
Automation doesn’t really need an introduction. It’s a fundamental concept that many industries and markets have already embraced since it offers, at the bare minimum, reduction in costs, increase in speed, reproducibility of results and upskilling of personnel.
What varies greatly however, is the perception of what automation is or should be. In the chemical industry in particular, an industry that self refers to as “a dinosaur industry”, automation tends to refer to streamlining action tasks rather than full processes. And this really matters.
For example, having automated stirring or heating/cooling is considered automation by many, even though the chemist still has to spend time setting up the reaction and carrying out reaction activities, such as additions, manually. And then executing all of isolation and purification, also manually.
Peptide synthesis is another popular example that is considered automated, even though chemists still have to spend 2-3 hours setting up these systems (preparing solutions etc) and 1-2 days carrying out purification manually.
Another popular, task specific, automation is column chromatography, which does as it promises, your column purification (which is great because every chemist hates doing this manually!), but the chemist still has to spend their time carrying out the reaction and isolation manually before getting to the column purification.
But is this just semantics? Even though these systems only automate tasks or parts of the process, isn’t this a form of automation anyway? Well, it does matter and here’s why.
Automation is meant to decrease costs and increase speed. Automating only one task out of the process can momentarily alter costs and speed, but not significantly. You wouldn’t review your business finances because you bought an automated column system.
Their impact is not significant enough to create change on an organisational level, like in revenue and profit margins. Furthermore, automating tasks only, doesn’t guarantee reproducibility or upskilling of personnel, which are two factors that can also fundamentally alter business operations.
Automating processes (instead of tasks) however, can completely transform a business and it’s operations. From finances to technical benefits, if used properly, the impact is profound.
In chemistry, true automation should be, end-to-end process automation, including recipe writing, setup, synthesis, isolation, purification, even data collection, cleaning and writeup. This type of automation moves beyond single tasks and focuses on an entire process making it cheaper, but even more importantly, making the data more reliable while giving projects defined timelines. Of course it also offers a massive boost in speed while upskilling chemists to more impactful and intellectual work, but it also promises accumulative effects, scientifically and businesswise.
Carrying out some tasks manually and others automated, makes the data unreliable and impossible to standardise while also not ensuring reproducibility.
For example, if a chemist carries out the synthesis of a reaction in an automated fashion (e.g. heating/cooling, additions, stirring etc), the out comes can still vary greatly in quality if the isolation and purification are executed manually. Manual labour errors, differences in skill and knowledge (see our previous post on reproducibility) and even environmental factors (room temperature today is different than yesterday, moisture and light content vary etc) can make automation of a single task unimpactful. Every single task that is connectively automated increases the benefits of automation exponentially until an entire process is fully automated end-to-end.
Unfortunately, full end-to-end process automation is rare in the chemical industry but can be found in some high throughput screening systems, flow systems and some cartridge systems. Of course, also CheMastery’s system.
All of these systems can impact your operations and business significantly if used correctly and some of them can be combined for even further accumulative effects. Which is best to choose highly depends on your KPIs, purpose of automation and even which part of the chemical lifecycle you wish to automate. We will explore which system is best for which application in another post, or contact us for a free consultation.
If you want to see what CheMastery’s end-to-end automation looks like for your business, contact us for our free Profit & Loss calculator.
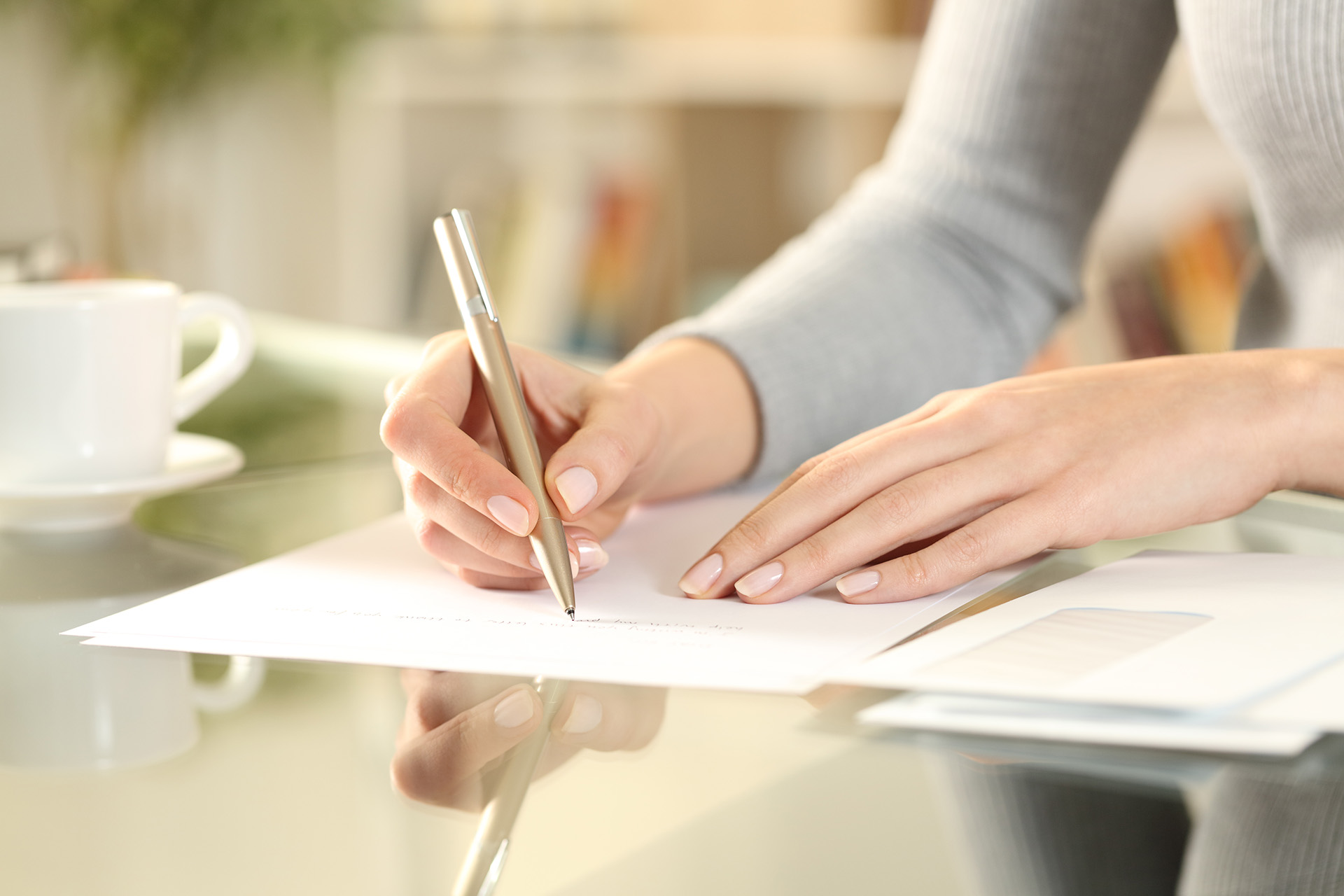
A Letter to Chemistry
A letter to Chemistry
Written by Dr Anna Andreou, Co-founder & CEO
Science is all about passion.
Passion for discovery, innovation, knowledge and pushing the boundaries. We are humans and we are curious. We are driven to explore, learn and make the world a better place.
I wanted to be a scientist ever since I can remember. As a child I used to closely study and tried to understand everything around me. That child curiosity created a drive to ask “why” about everything.
Years passed and I discovered that my calling was specifically in chemistry. Understanding why things work or do not work on a molecular level, was extremely fascinating.
After 8 years at university, I completed a Bachelors, Masters and a PhD in Chemistry. I was incredibly lucky and blessed to study with world class lecturers and people that I would truly call scientists. I learnt so much in the process about science, chemistry, the world and even myself.
Sadly, in the process I also learnt that practical, everyday science wasn’t this romantic idea that I had in mind.
As a Research Chemist working in different Organic Chemistry labs for over 10 years, I used to spend 60% of my time executing what I would describe as, manual repetitive labour. Set up another reaction, do another filtration, another liquid-liquid separation all in hopes that there isn’t a column to do as well. Noone likes columns.
But the reality of the job is that chemistry is practical. And the vast majority of the job will have to be practically executed. But, that’s not why we became scientists!
We become scientists to innovate and use our intelligence, to understand and add value.
That's truly what sets humans apart from other things, like machines. But somewhere, somehow, the chemical industry lost that passion.
Today, laboratory chemists are often “hands in the lab” and somehow that became acceptable. We tolerate issues that come from manual execution, like irreproducibility, slowness and high costs because it happens to everyone. And bizarrely, we tolerate these problems so much that even though everyone agrees on them being problems, very few organisations actually track the research impact or even the cost.
How much research potential is irreproducibility costing you every year?
How much more research could you have done in a shorter period of time if that wasn’t the case?
Why is everyone content with calling the chemical industry “a dinosaur industry”?
Why does lab work still look the same as 150 years ago?
Have you ever wondered why chemistry is one of the lowest skilled worker industries in productivity, salaries and employee added value?
If COVID taught us anything, it must be that science, technology and innovation should be at the forefront of everything we do.
I founded CheMastery because I believe that chemists should be enabled to be critical scientists. Chemists should be the masterminds that focus on the innovative parts, the thinking, the strategy! Nothing can compete with human intelligence. Even AI and all of today’s fancy tools, it’s human intelligence that made them.
It’s time we lead with science again.
Sincerely,
Anna
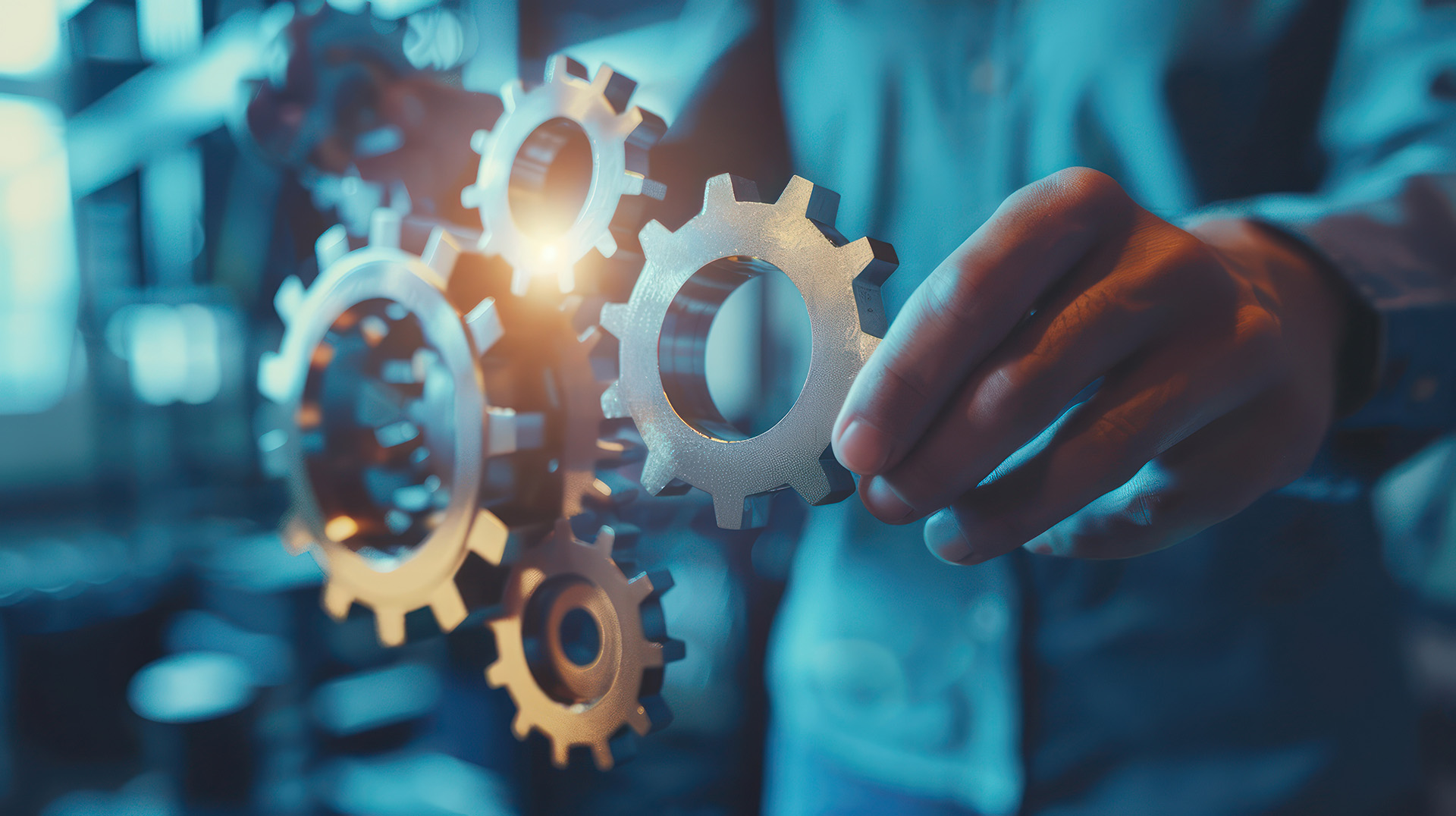
The Value Proposition of Automation
Automation is not a new concept. However, while is has been widely adopted in other industries, chemistry has largely stayed behind. The reasons for this are interesting and worth exploring in another post but for now, let’s look at the value proposition of automation in chemistry.
In general, automation reduces costs, increases project speed and ensures reproducibility.
The exact value proposition, however, depends on the specific automation solution.
Lower costs
Automation is cheaper than manual execution. It allows you to cut costs, increase profit margins, and upskill your chemists to fundamental research tasks, increasing the value added per employee, thus the value of the business.
Machines are great at doing the same thing over and over again, providing a reproducibility guarantee. Even if you have a high manual execution reproducibility rate of let’s say 95% success (really well done, that’s significantly higher than market average!), a reaction can still be reduced in cost by 50% when automated.
Productivity boost
Automation can increase throughput by running 24/7 while being accurate and precise.
A machine that works 24/7 can produce a minimum of 8760 hours of lab work a year and depending on the solution, produce hundreds to thousands of reactions.
Our customers told us that on average, a chemist spends about 903 hours a year in the lab, carrying out research or manufacture, and produces on average 5 reactions a week.
This results in a minimum 24x productivity uplift, returning a 50x upskill multiplier for the chemist, in terms of time invested vs work and data produced in return.
Productivity in the chemical sector is nowhere near where it could be. For example, here in the UK, this has even been noted in the Government’s Industrial Strategy Whitepaper. However, it would be unreasonable to expect it to be as high as other industries that already adopted automation.
Upskilling chemists means higher value added employees
While there are many values that come with automation, some of which we explored above, we believe that the highest value of automation is in upskilling of personnel. Upskilled personnel are not only happier, more productive and more loyal (reducing recruitment and onboarding costs), but also add more value to your business.
No matter what you’re currently working on, research or manufacture, according to our market study, your chemists are spending 50% or more of their time carrying out repetitive laboratory tasks. Do you really need a PhD in Chemistry to setup another reaction or carry out another filtration? Upskilling highly trained personnel to fundamental research tasks which involve their intelligence rather than “hands in the lab” execution, significantly increases the value added per employee and hence the value of the business.
Automation systems should support chemists, preparing materials and executing work for them, even out of hours. For example, making starting materials and intermediates ready for them when they are back, making libraries, carrying out DoE and other optimisation work, scale-up studies and even direct research to lighten the practical load as they strategize next steps.
Increased Speed and Project Success Chance
Speed is not just money, it’s also increased project success chance. Not only do you complete a project faster (and go to market faster and utilise patents longer) but you can also run significantly more experiments in that time, increasing your chances of success.
Lower chemical waste
Automation often reduces chemical waste, especially when tied to reproducibility. Instead of repeating a reaction a couple of times to get it right, machines only need to perform it once, allowing you to focus your resources on improving and understanding the chemistry.
Benefits of automated labs
There are many future benefits that are not instantly obvious while automation is not commonplace.
One such benefit is that automation requires a different infrastructure that is significantly cheaper than manual labour infrastructure. For example, one of the most expensive parts of running a manual chemistry lab is the air extraction of the room and the fumehoods. However, fully sealed and ventilated machines do not require room extraction or laboratory infrastructure. One could easily have them in a cheaper industrial estate, lowering rent and other infrastructure requirements like space. Machines can be stacked and extracted specifically, reducing costs.
Drawbacks of automation
If you are concerned about automation reducing jobs, we do not believe that will be the case overall. Some, small businesses, might choose to survive during difficult financial times by employing automation to cut costs, but humans will always be required in research. As it is widely known, there is a general lack of STEM employees and according to a study in 2023, by the Eurobarometer, there is specifically, a lack of R&D experts and lab-workers. Automation can be the solution here, offering lab-work and upskilling chemists to R&D experts. Chemists want to be scientists after all, not hands in the lab!
We will explore the shortage of STEM employees in another post however, it is worth noting that we believe that one of the many reasons (but not the only) for this is the low salaries offered in the field. Automation could offer a partial solution here too, as it has increased salaries in other markets, due to employees being upskilled and carrying out higher value tasks.
Do you know anyone who left chemistry for the software or finance sector?
This was a very quick and summarised overview of the value proposition of automation. Of course, there are a lot of other, solution specific, values which have not been explored here. In our case, for example, CheMastery’s system offers integration to workflow, scale-up, DoE, capture of skill and knowledge and a lot more.
If you are interested to dive a little deeper or want to understand the formulas and where some of these numbers come from, contact us for our free Return on Automation Investment calculator or talk to us about your needs.
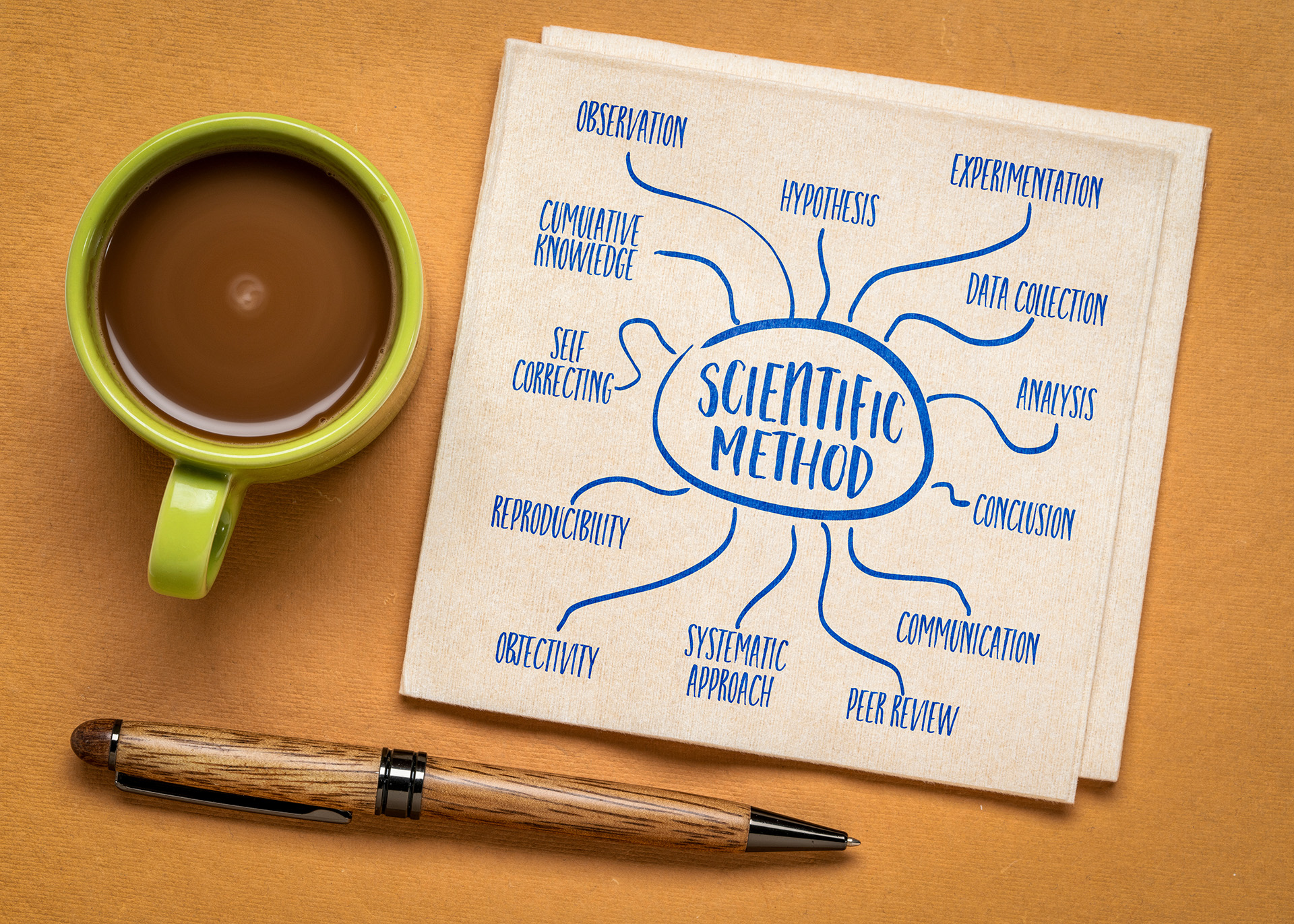
Chemical Irreproducibility and Where it Comes From
Before we decided what to focus CheMastery on, we carried out a market study asking chemists of different seniority, geographical location and chemical discipline:
“What are the top 3 chemistry problems?”
The question was purposely vague to avoid biasing or leading the question. And the results were:
In first place: irreproducibility,
second place: cost/time inefficiency
and third place: scale-up
No surprises here.
Unfortunately, irreproducibility shouldn’t come as a shock to anyone. It is a big problem and has been around for a while. Every scientist you talk to, chemistry or other industry, will have stories to share.
We were also of course, not the first to spot this. There were many people that talked about irreproducibility and many published studies that captured this before CheMastery even existed.
One of the most famous articles was published by M. Baker in Nature in 2016 which showed that ~86% of chemists experienced irreproducibility. It also looked at other STEM disciplines which also admitted to the problem but fared a little better. Another notable advocate for these issues is Derek Lowe, check out his “Thoughts on Reproducibility” article. But the list doesn’t stop here, there are many more.
Frankly, we’ve never met a chemist who hasn’t experienced this, and we’ve talked to many biologists who tried to argue that they have it even worse than chemistry.
What an embarrassing debate to have!
However, it was the rest of our conversations with these chemists that were particularly interesting.
While the vast majority of chemists agreed on irreproducibility being a problem, there were fundamental differences in where the blame is pointed and what they do about it.
These differences in thinking and action (or lack of thereof) are incredibly important not only for understanding the problem but also in how they shape the future of chemistry.
Some chemists we talked to blamed irreproducibility on the quality of materials supplied by vendors, others blamed their colleagues, some blamed the flawed academic peer-review publication system and many of them were honest enough to admit that regardless of the multiple flaws in the chemical supply and information chain, they also couldn’t reproduce their own work sometimes.
The reality is, all of the above are true. Such fundamental problems are often complex and multi-sourced. So, let’s dig a little deeper.
Suppliers
Supplier batch-to-batch reproducibility of chemicals is not always reliable and there are many contributing factors to that. The most straightforward case and arguably the main challenge is how these materials are made.
It is important to note first that we are referring to specialty chemicals here, and by specialty chemicals we mean materials that are made on the milligram, gram or low kilo scale. Basic chemicals that are made in larger quantities are often made in chemical plants which follow some procedures and regulations, and hence are often reliable.
Specialty chemicals however, which account to ~99% of unique molecules made, are often synthesised and purified by manual execution and this comes with its challenges. Not only in batch-to-batch quality but also cost, speed of delivery and other issues like traceability and transparency in how and where they are made.
Another noteworthy factor is that many vendors sell chemicals that are not made by them, and this leads to inconsistencies in information, quality and execution. Very few suppliers check all their materials via analytical methods to verify or even guarantee quality, even fewer then even share this information with their customers and similarly, very few have full knowledge of the chemical pathways and methods that created them.
However, the knowledge of how a material was made can be extremely powerful, especially in the reproducibility context, as there can be cases where it makes a difference. For example, traces of metals present from the synthesis of these materials (or other impurities that are hard to spot in analytical data) might be destroying or catalysing a future reaction or application. And for some customers, the method or location of manufacture might be part of environmental, sustainability or other policies too.
Irreproducibility in manual execution and between colleagues
Difficulties in reproducibility between colleagues, departments or companies are also very common and stem from many different factors including: differences in training and interpretation of procedures, differences in experience, skill and knowledge, attention to detail, unstandardised experimental descriptions, unmonitored day to day variations etc.
Most of these are quite straightforward to understand and notice but much harder to solve. Chemists coming from different Universities or other training programs will have vast differences in knowledge and even in practical execution. For example, two chemists will often setup a reaction differently: do you start the reaction time when you set it up or when it’s actually refluxing, do you clamp the reflux condenser or not, do you add via syringe, pipette, a flask or a dropping funnel etc.
Some decisions are more fundamental and impactful than others, but the tricky part is that we don’t always know which of these factors are important and which are not, in every single case.
For example, in some cases stir rate might make a huge difference and is especially important in scale-up and manufacture, but R&D chemists very rarely note or test this in their procedures. In other cases it might be the order of addition of certain chemicals that perhaps form an intermediate which then reacts with the third etc. The best bet for reproducibility and traceability (as well as future proofing manufacture) is to capture absolutely everything. But that is hard, some would even argue unfeasible, to document and execute manually.
If I gave you the perfect recipe that is 25 pages long and had every single piece of information you needed to reproduce something, would you read it? And would you follow it to the letter? Chances are you will skim read, interpret according to your training and execute some parts according to your experience. That is human nature.
Humans are great for intelligence but not for repetitive work, and chemistry is by its nature practically repetitive. Even when you do research.
Setting up another reaction, doing another filtration, then another crystallisation. The mental work might be new, but the practical work is the same techniques over and over again. The absolute majority of organic chemistry requires: heating or cooling, stirring, adding a reagent, an organic workup, a filtration, a crystallisation, column chromatography or distillation. These techniques are the workhorses of organic chemistry and with these you can make the majority of molecules.
How many more filtrations can you do before you master the skill. We get bored, we loose focus, we do things fast, we skim read papers. That’s what chemists do, that’s what humans do.
There are of course many other factors that contribute to irreproducibility, like for example the fact that environmental conditions are rarely taken into consideration.
Some reactions require a certain level of moisture even under inert gas. UV and how bright it is in the lab that day can make a huge difference as well as baseline parameters that are not that basic! A famous example that every chemist is guilty of is setting up a reaction at room temperature. Room temperature has become equivalent to “I haven’t used external heating or cooling” but how many chemists actually note if it was, by scientific definition, 20 degrees Celsius on that day? There are many other examples like this one and in some cases they can be very impactful.
A lot of these execution variations also explain the phenomenon of the “golden hands”. In case you haven’t heard of this, “golden hands” is this one chemist who is incredibly good at executing a particular reaction when everyone else fails at it. Scientifically, there is no reason why that should be the case other than they know or do something that the rest of the chemists don’t. Something about the way the procedure is executed is different and it is not captured in the experimental description, leading other chemists to be unable to reproduce.
It makes skill and knowledge person-specific, rather than organisation specific, and for the business minded out there, this costs a lot of money and time.
The lack of industry-wide standards on how we communicate and describe experimental procedures is a big part of reproducibility. It widens the already different ways of executing a reaction and allows room for interpretation. Science should be factual. “Science is show me, not trust me”, another great post on reproducibility, by Philip B.Stark at Berkeley.
Here's an example from our CEO: "I’ve previously encountered an experimental from the literature which did not specify a temperature and my colleagues failed to produce the material while following the procedure. When I read it I could immediately spot the problem, which was that it should have been executed at-78 degrees Celsius instead of what my colleagues assumed (which was a fair assumption): at the lack of temperature specification, try room temperature. This information was obvious to me because I had experience in that reaction type, but my colleagues didn’t. While experience is important and makes a huge difference, in a world where trillions of reactions exist in the chemical space, it is impossible for chemists to know it all."
Before you dismiss this example as a bad chemist, who after all doesn’t mention one of the most fundamental of things, temperature. We did a study of chemical databases and found that a significant amount of experiments do not specify temperature (% varies from database to database).It’s not just a single bad chemist or an attention to detail issue or an assumption, interpretation or experience problem.
It all comes down to lack of standardisation.
Documentation and communication have to be standardised even between specialised personnel.
These are some of the reasons why Good Manufacturing Practice (GMP), Chemistry Manufacturing Controls (CMC) and International Organization Standardisation (ISO) processes exist but unfortunately, these are rarely followed in R&D settings and many of them are generic and organisational rather than material specific.
Lastly, as this post is getting long, through our chemist interviews we also heard about another manifestation of irreproducibility, this time between organisations.
Contract Research Organisations (CROs) and Enterprises alike both told us that when they work with each other they often have difficulties in skill and knowledge transfer.
For example, a Pharma pays a CRO to develop some work for them. It usually takes months (sometimes longer) and when the work is delivered and the Pharma tries to continue that work internally, they can’t always reproduce it. Similarly, we’ve also heard about this problem from CROs who are upset with being blamed for irreproducibility when it might have been the Pharma’s chemist fault.
We also heard from Enterprises themselves.
It's very common for organisations to have difficulties reproducing work between their departments and between sites, sometimes in different countries.
It’s a combination of differences in batch of materials, chemist skill and knowledge, experience, assumptions, lack of communication and execution standards, the inevitable flaws that stem from manual execution, environmental differences etc.
Irreproducibility in peer-reviewed publications
The peer-review system for academic publications is flawed in many ways. It’s not a secret and yet this is another fundamental problem that very few in the industry are trying to change. However, this is a large and complex subject for another post.
If you want to read more about this we recommend the article “Is the staggeringly profitable business of scientific publishing bad for science” written by Stephen Buranyi and published in The Guardian in 2017.
Irreproducibility is a large and complex problem and as we explored, it can have many different manifestations and often multiple reasons at the same time.
However, although this is a problem that the industry generally agrees on, very few businesses actually track its impact on their cost, speed of discovery and retention of skill and knowledge.
The good news is that digitisation and automation of chemistry addresses all of the above. We experienced these problems first hand multiple times and with these in mind we created an end-to-end automated system which standardises the information of an experiment, both in content and language, and then executes the work reproducibly while using scale-up processes to ensure manufacture applicability.
Today’s reality requires chemists to do more. Discover more, faster, cheaper, better. This fast frenzy combined with manual execution is a recipe for disaster.
Industrial revolution created automation to lower costs, improve standards and meet the demand. Why isn’t science doing the same?